Hey Boys & Girls,
So, let’s get started.
Nov 21st 2010
Many of you may be saying to yourself PICTURES!!!! So enough of this reading how about some pictures!!!
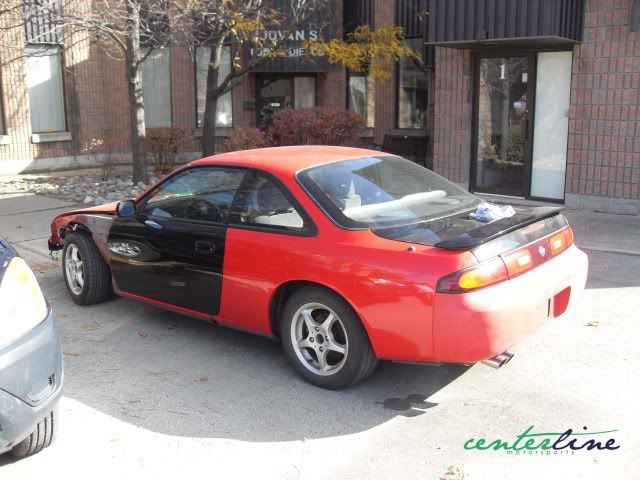
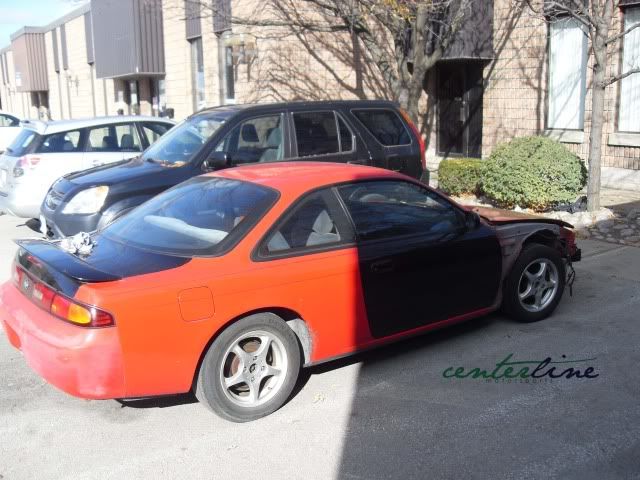
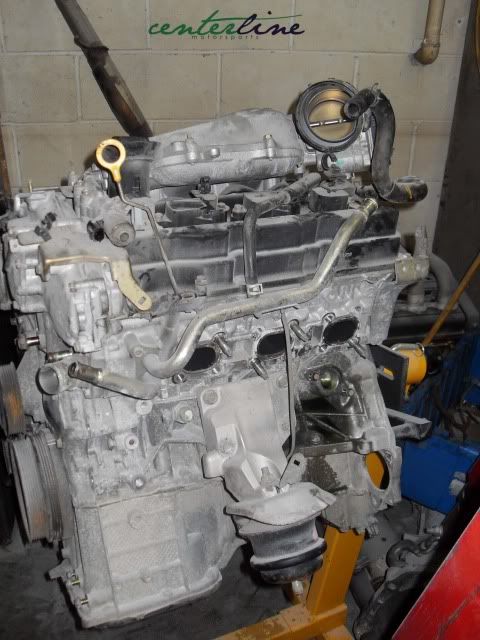
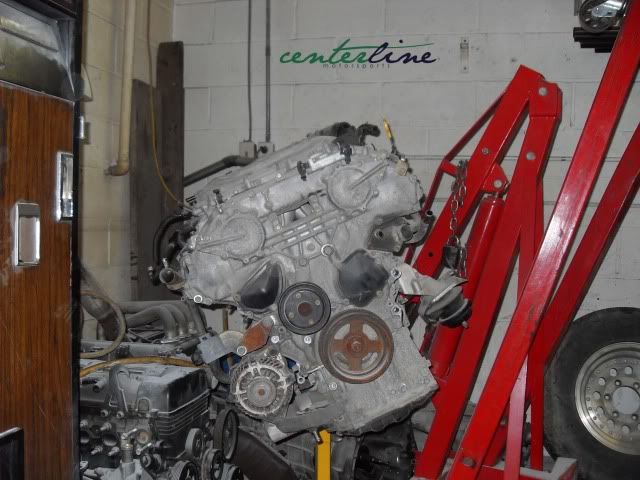
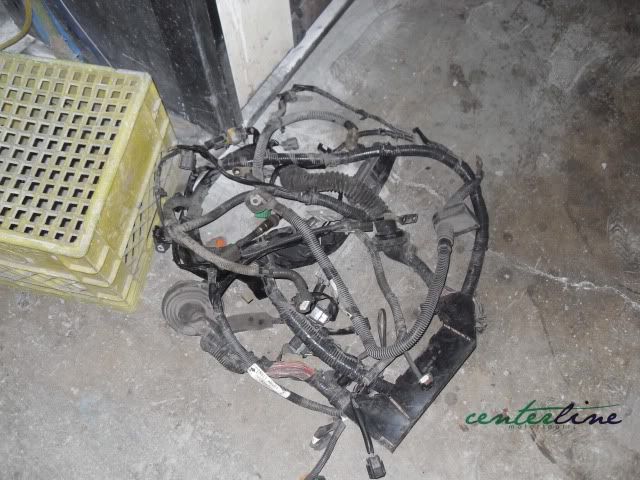
Now that you have seen the starting grounds of what I hope of a really good project I would like to post up some of the recent fabrication tools I picked up in the last couple months.
I picked up a few nice things to help me do almost anything.
JD Square Model 32 Bender [Bought this during my last build]

Precision Tig 225 & Cool-Arc 40 Water Cooler [Bought tig welder after last build, water cooler is new addition]

Metal Bandsaw
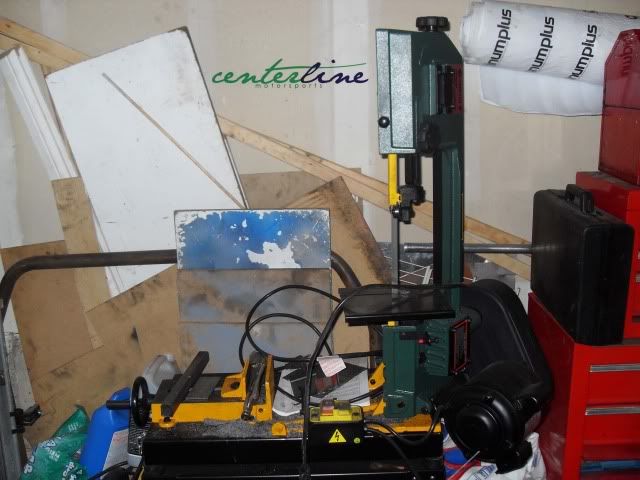
60 Gallon Compressor
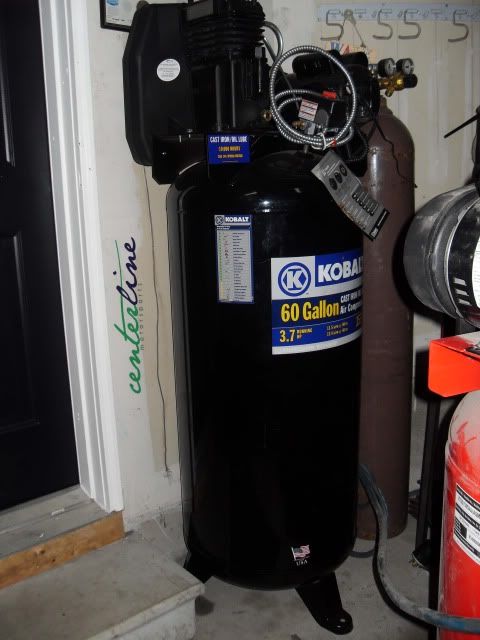
Torchmate Plasma CNC Machine & Hypertherm Powermax 45
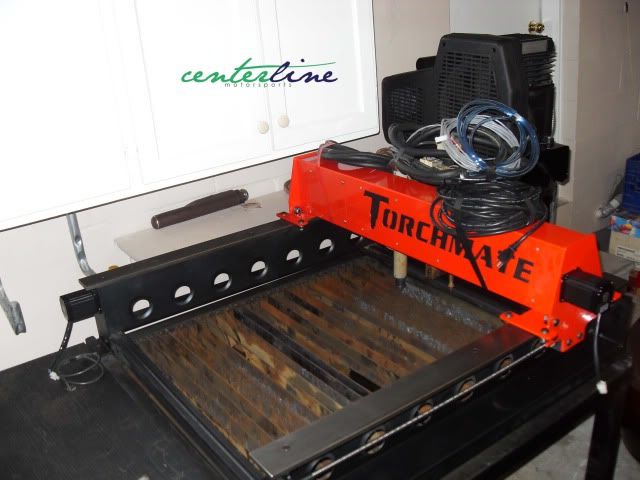

The best addition to everything was the pickup of my new [well old] Truck
Ford F350 Crewcab Diesel Dually [Getting some paint and wheels next spring]
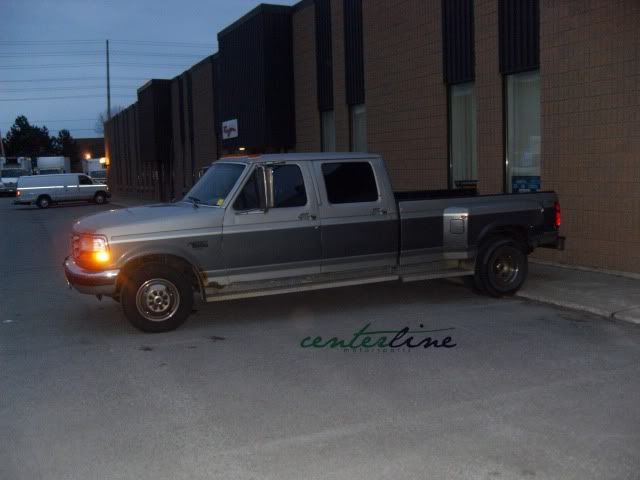
That’s all I got for today! I should have more posted soon.
STAY FRESH EVERYONE!
I would like to start by saying I have been lurking around the site for a bit since my last big build. I haven’t been very active on the forums, but have always been looking for a new challenge [Project]. Some might question my ethics as to why another 240sx….or why didn’t I just keep the original one I had with the 2JZ. I must say I did try and find a new platform to work with and move away from the older chassis of the 240sx, but the problem that came from that was I couldn’t really find anything that interested me. I really wanted to get into an evo, but starting price plays a really big factor in everything and it’s always nice to have a very basic base as a starting point.
The plan for this build thread will be the same as the last one. I plan to keep everything up to date and make sure to post everything in orderly fashion just as the last one. I know many of you may think how can I possibly top the last build….well that’s a good question, but when it comes down to it there is always something that could be done better than the last one. I already have a major parts list of things I need to do, fabricate, buy and whatever else could possibly be done. The only slight difference between this build compared to the last one is I plan to build, fabricate as much as I can in-house and have very limited out sourced.
I hope with all my new and interesting fabrication equipment I’ll be able to make just about anything. It may all seem like a big task to complete, but with the help and support of friends and family anything is possible.
So, let’s get started.
Nov 21st 2010
The day begins as I pickup my new project off my buddy Stefan [Foot]. He had plans of building a nice street car from this very clean chassis, but due to circumstances he had to bail. I personally think he couldn’t have sold it to a better person
. Now that we have some history out of the way we move onto the car. The car itself has a very small rust spot on the driver side rocker and some light rust in the engine bay, which I would say is typical to most 240sx. To my luck this was a Texas car so the frame rails are mint, but doesn’t really matter since its unibody. The only downside to the whole car is that its auto so it gives me some work to swap it over, but nothing to major compared to everything else that needs to be done.

Motor selection took some time to decide. I had been juggling the idea of this whole project for quite some time and it was all to be completed with a VQ35DE. The motor itself is not the most appealing motor setup to ever come from Nissan, but I thought this time I would keep it to a Nissan power plant. There were many more possibilities as to Nissan motors, but I just couldn’t pass the price I got for a complete motor set with only 50,000km. The next big question is to twin turbo or rock it one hundred percent naturally aspirated. I have been leaning more to one than the other, but I’ll be keeping that a secret until I reach that step in the build progress. I ended up disassembling some of the motor setup and didn’t have pictures of it all complete with everything on it, but in other news I ended up finding a nice 6 speed transmission for a really good price.
Many of you may be saying to yourself PICTURES!!!! So enough of this reading how about some pictures!!!
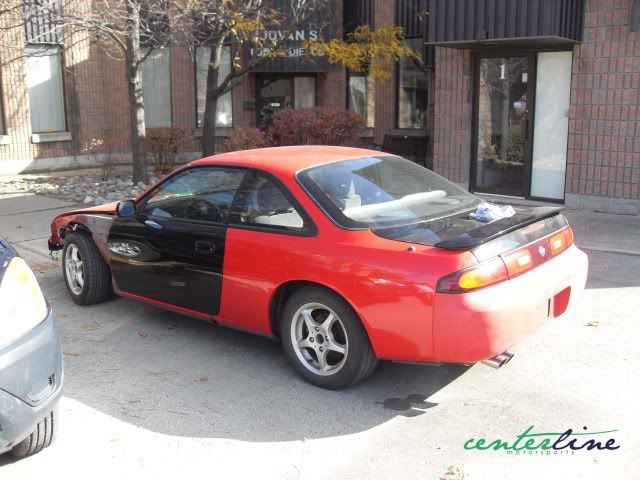
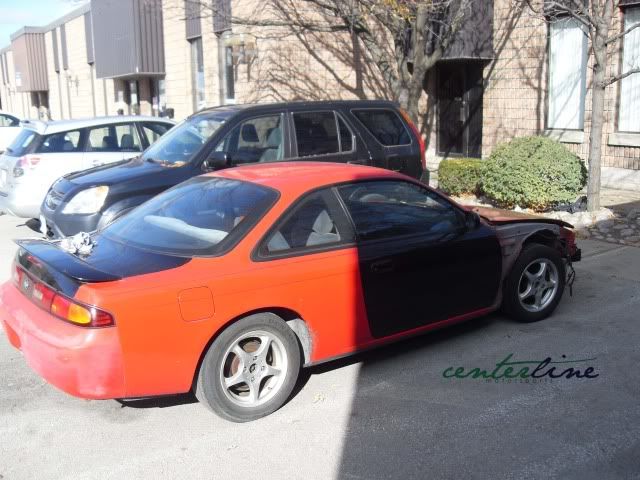
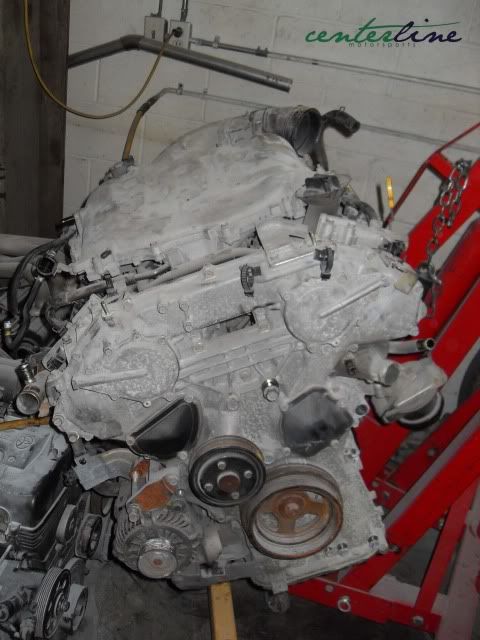
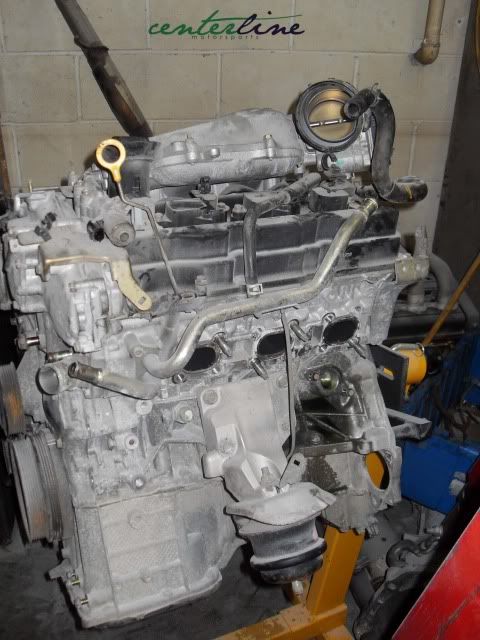
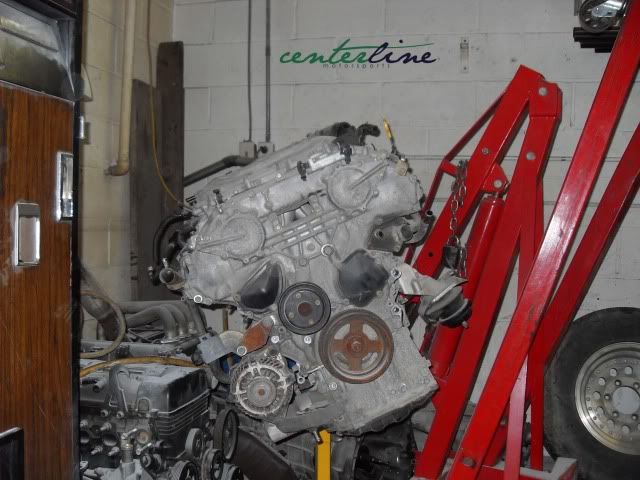
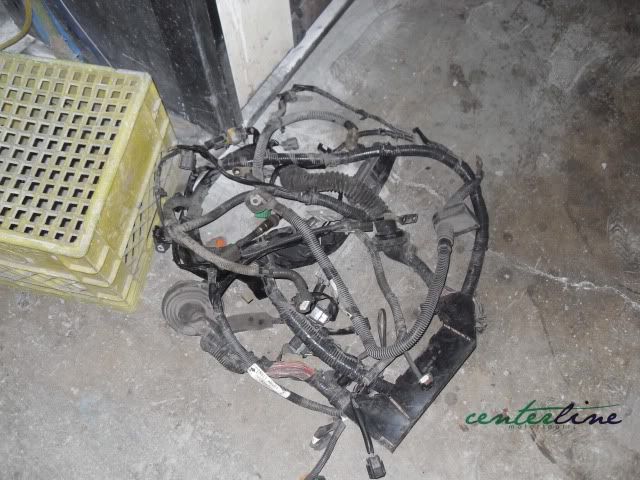
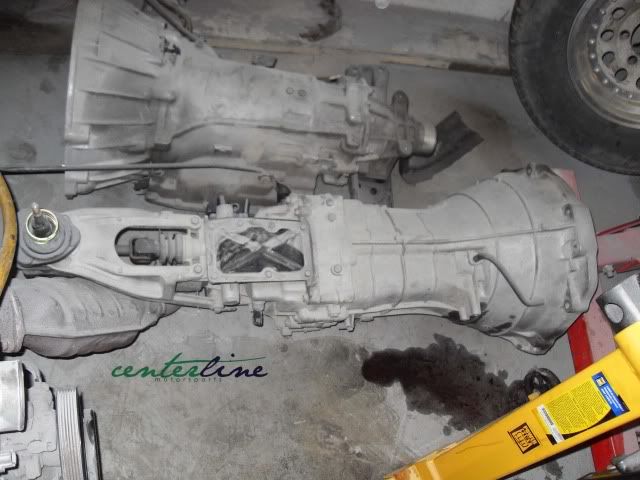
Now that you have seen the starting grounds of what I hope of a really good project I would like to post up some of the recent fabrication tools I picked up in the last couple months.
I picked up a few nice things to help me do almost anything.
JD Square Model 32 Bender [Bought this during my last build]

Precision Tig 225 & Cool-Arc 40 Water Cooler [Bought tig welder after last build, water cooler is new addition]

Metal Bandsaw
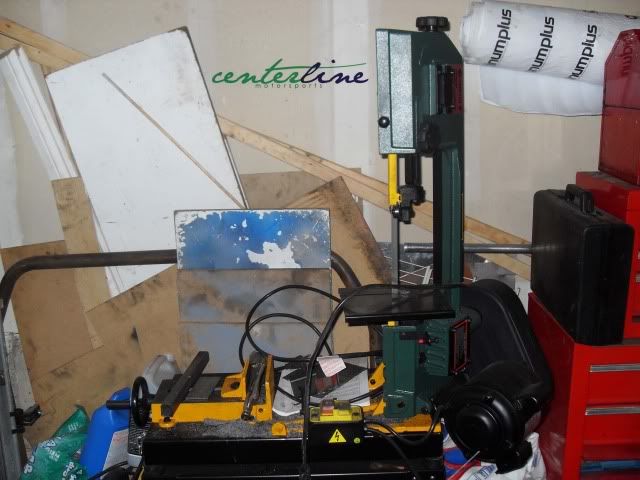
60 Gallon Compressor
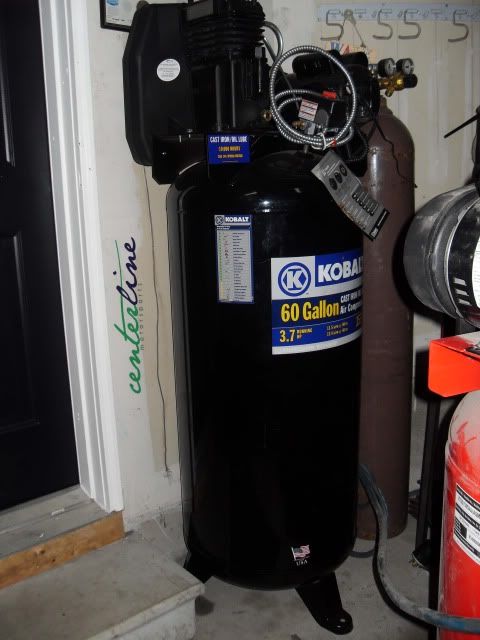
Torchmate Plasma CNC Machine & Hypertherm Powermax 45
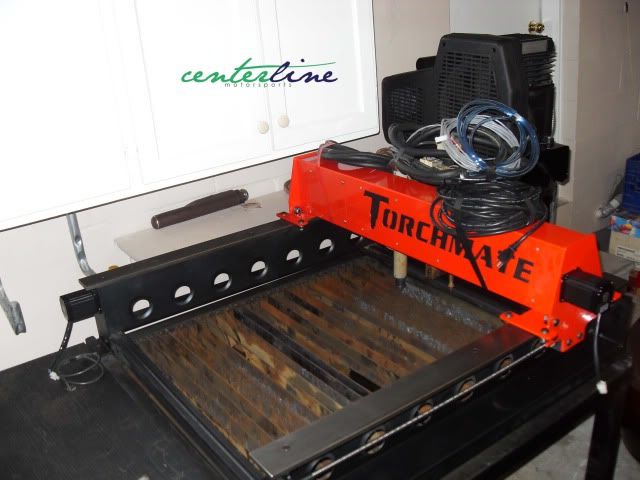

The best addition to everything was the pickup of my new [well old] Truck
Ford F350 Crewcab Diesel Dually [Getting some paint and wheels next spring]
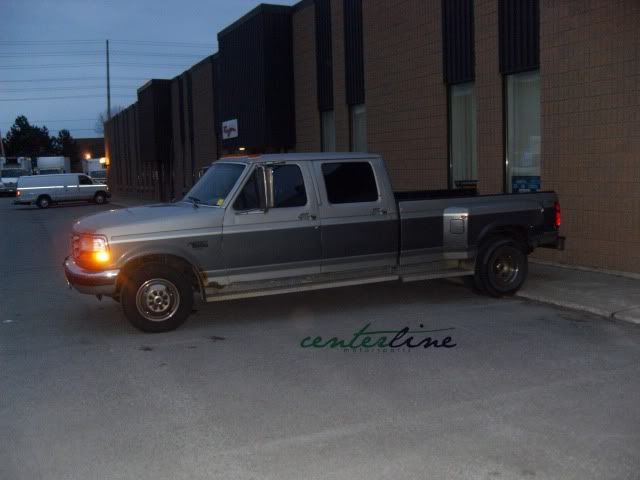
That’s all I got for today! I should have more posted soon.
STAY FRESH EVERYONE!
Comment