Last thing that needs to be done before putting the pan back on is changing out the oil pump gears to a set from Reimax.I will be using the stock 81mm pump for this.
Here is the pump off the block.
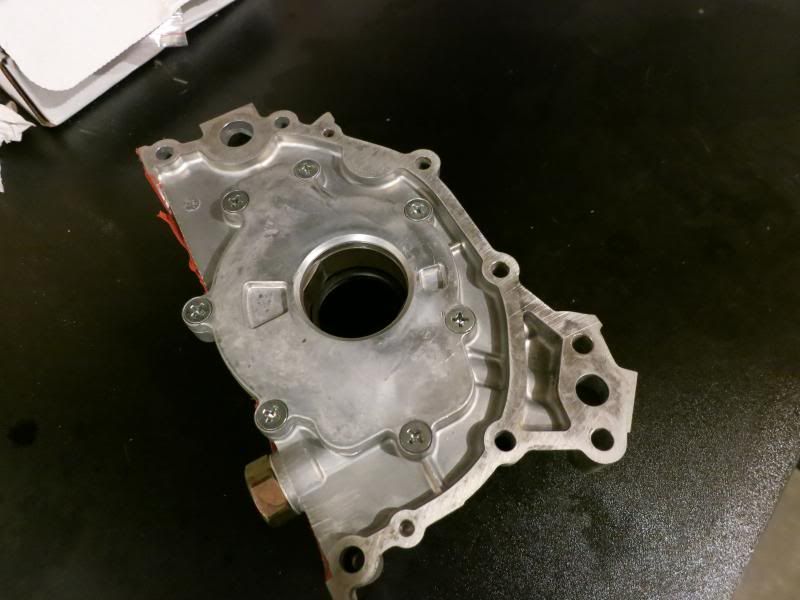
A few seconds later..note the absence of timing marks on the gears.
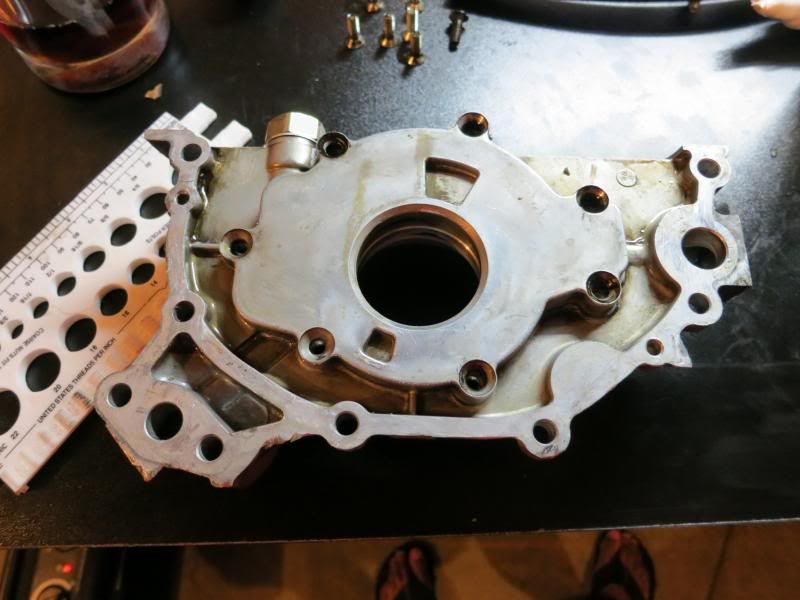

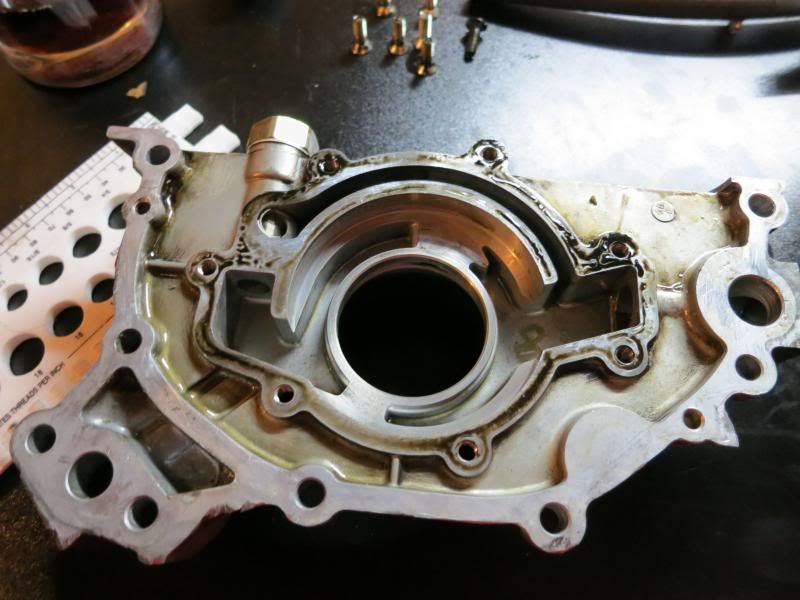
Here is the new set of 81mm Reimax gears.
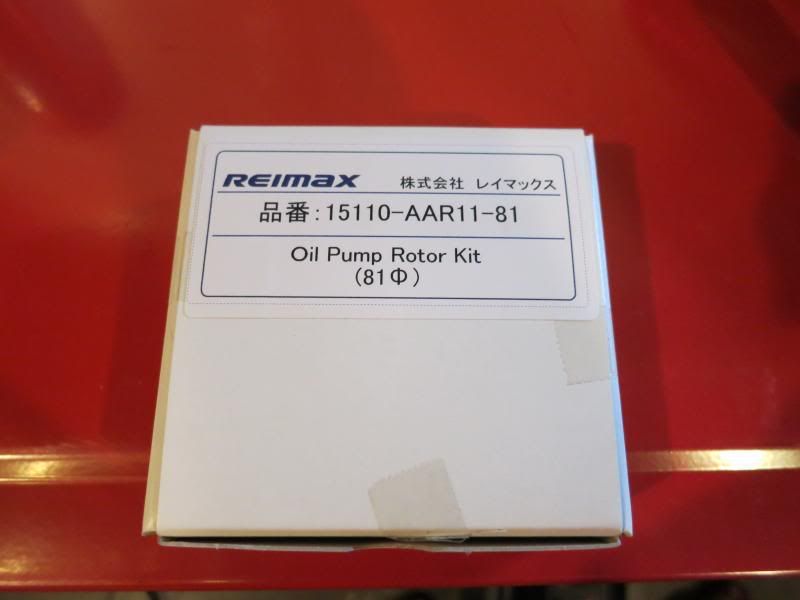
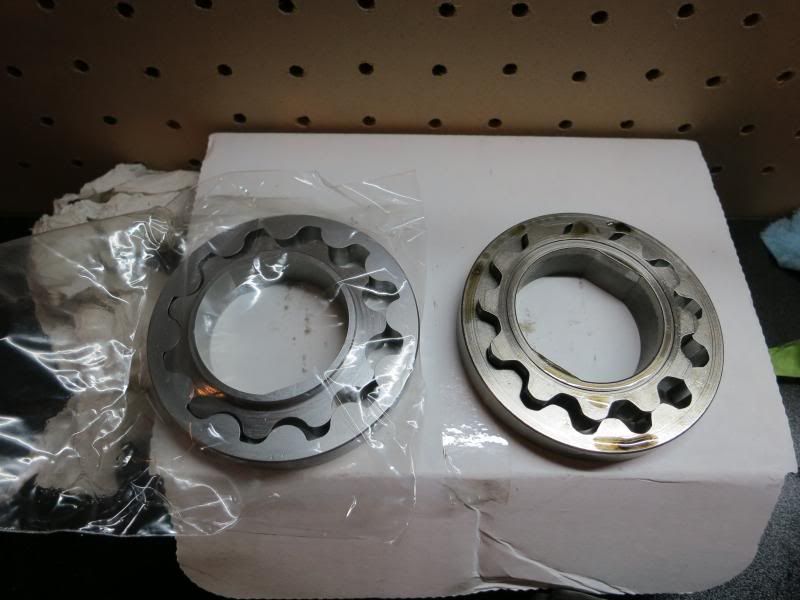
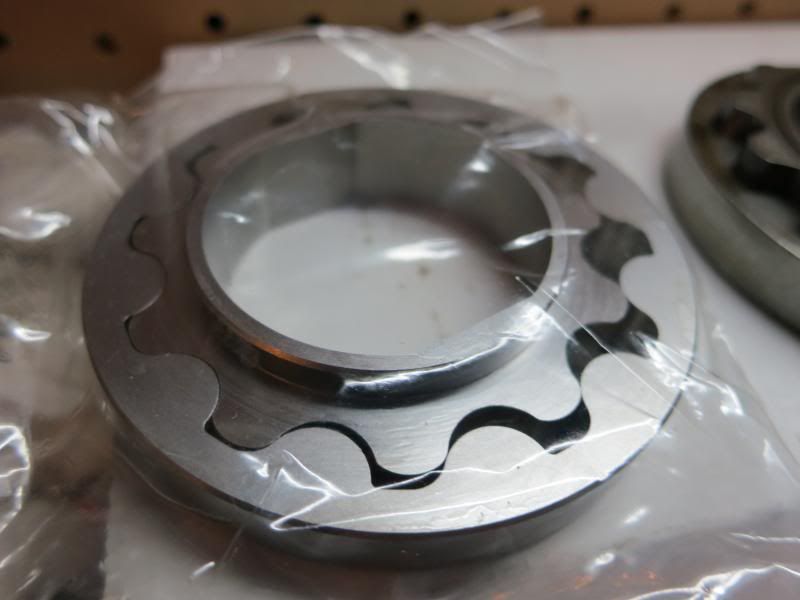
There's only one way for these to go to line up the timing marks.A light smear of oil went on before buttoning up the cover plate.
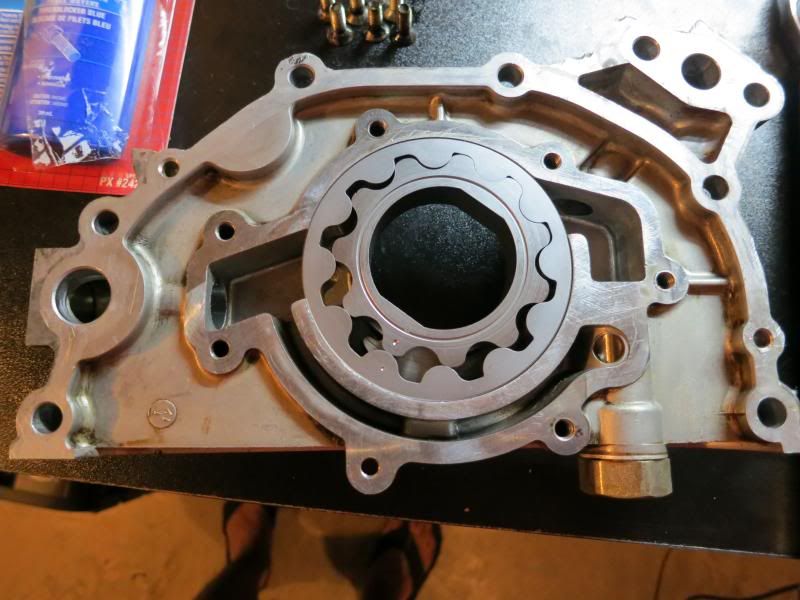
A light smear of medium strentgh blue threadlocker went on each screw. Didn't bother with a torque wrench on these so just went a tad beyond snug.
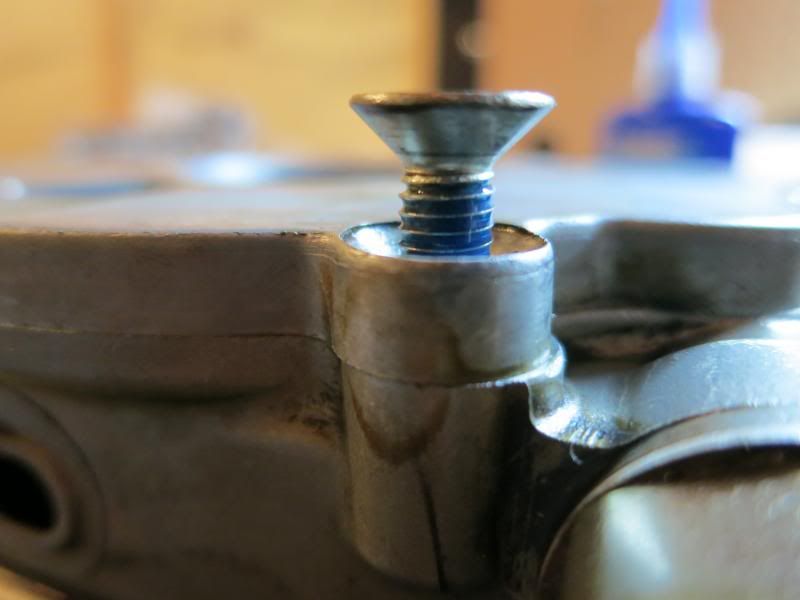
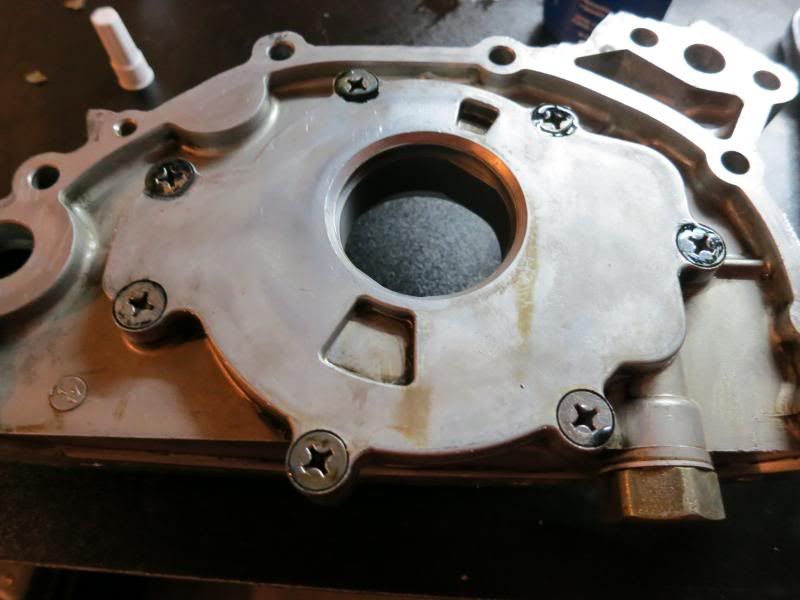
Next I installed a new oil seal. I just coated it in WD40 and pushed it in by hand till it was flush with the pump surface. I will coat it with oil later.
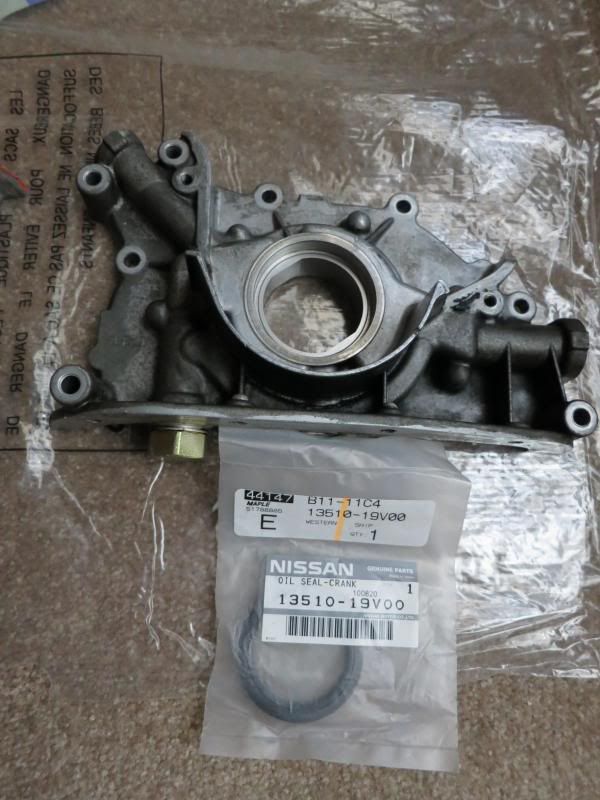
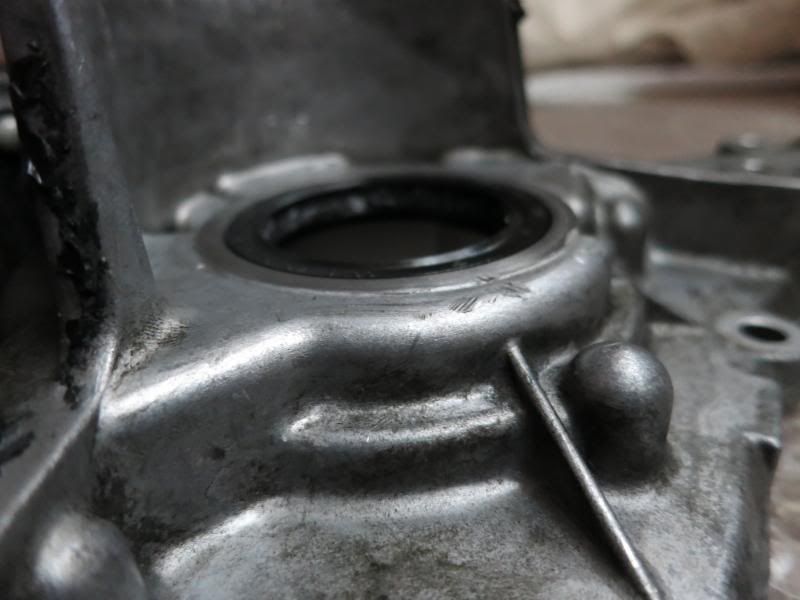
I then cleaned up the remnants of the RTV off the block.
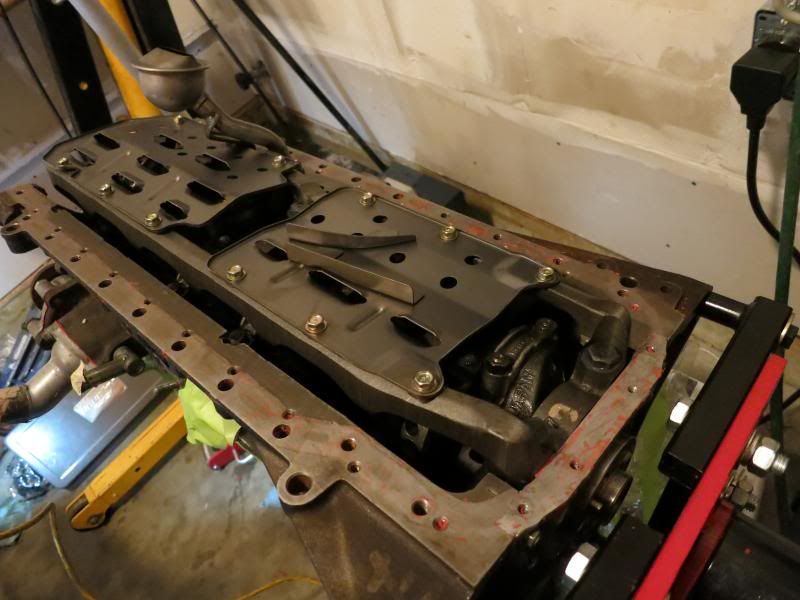
I then bolted up the oil pump to the block, using some gasket sealant of the pump gasket.
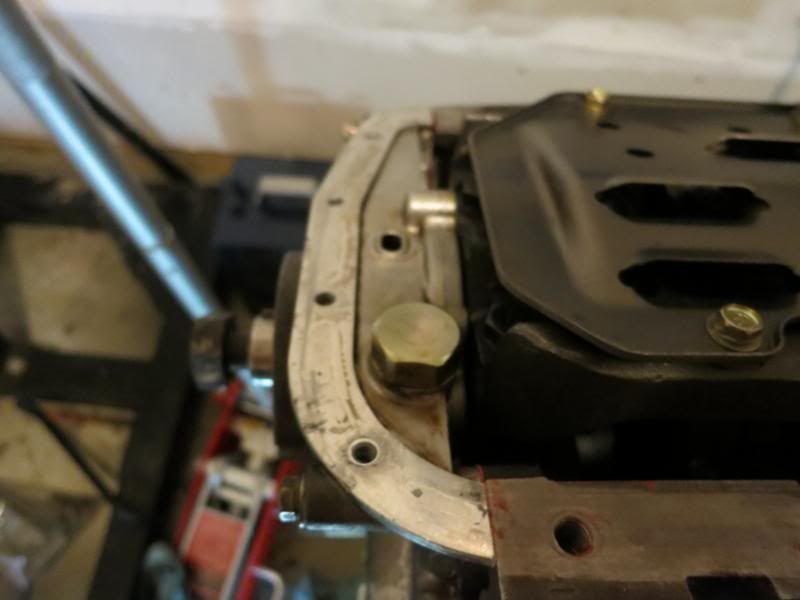
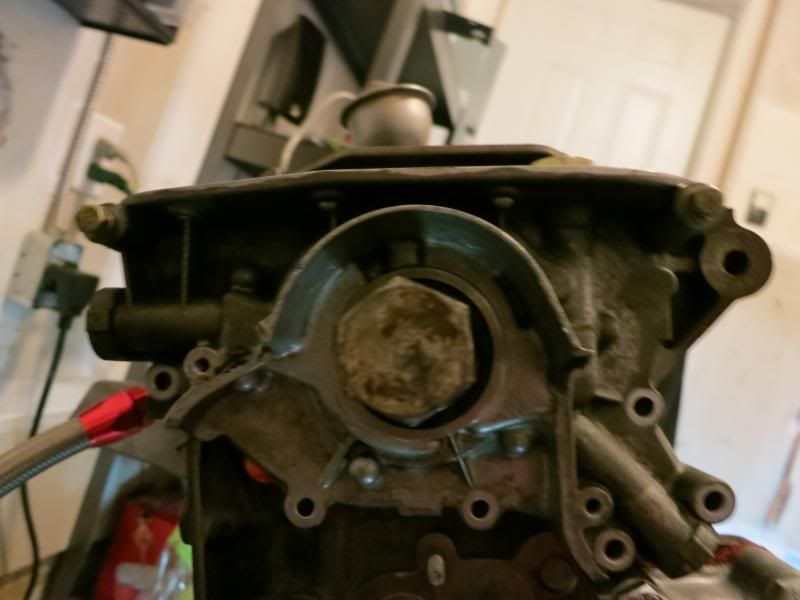
Used some of the good old orange RTV and went to town with it.
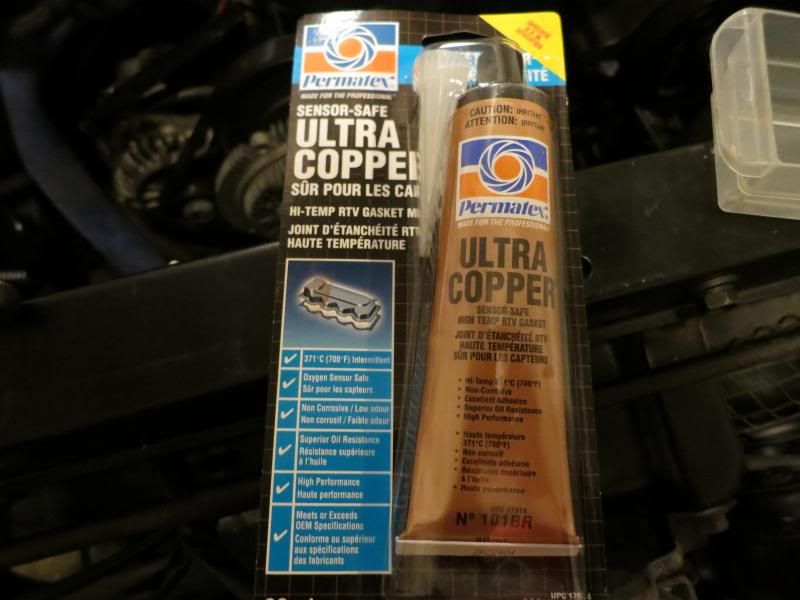
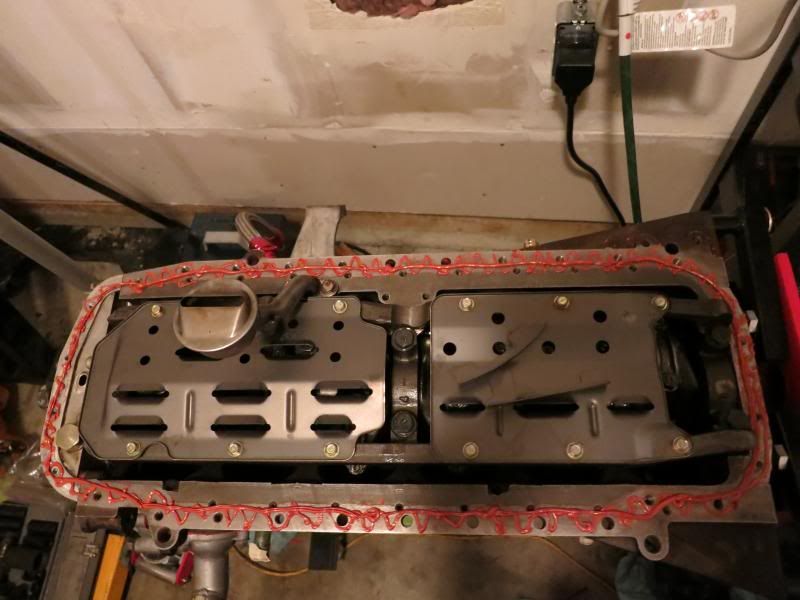
Then put the cover back on and torqued it up to spec.
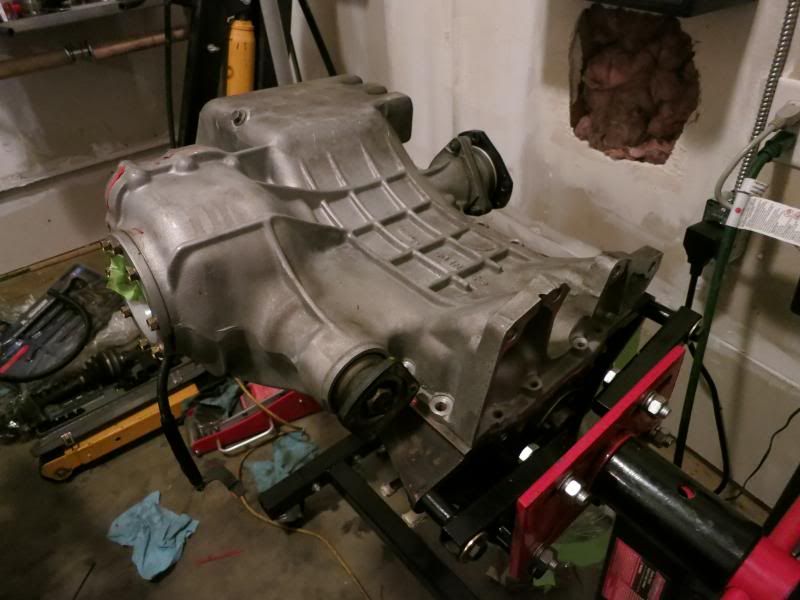
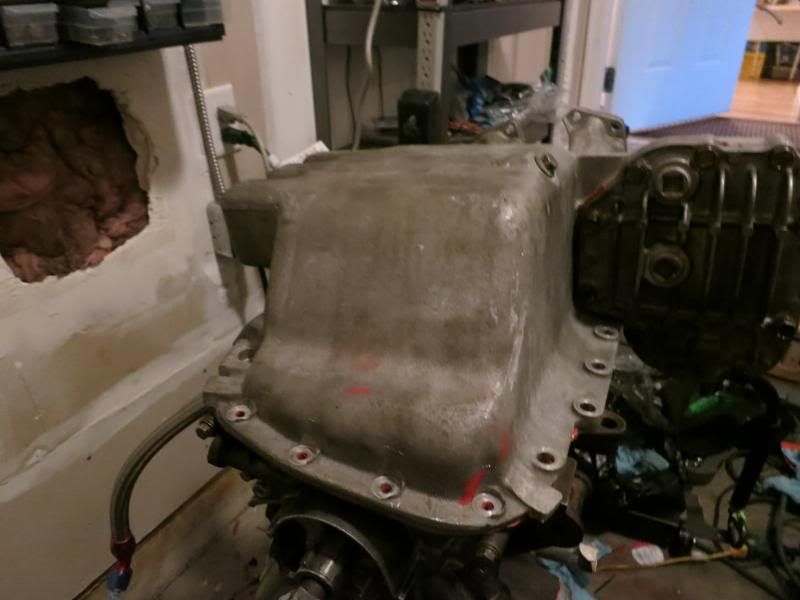
Here is the pump off the block.
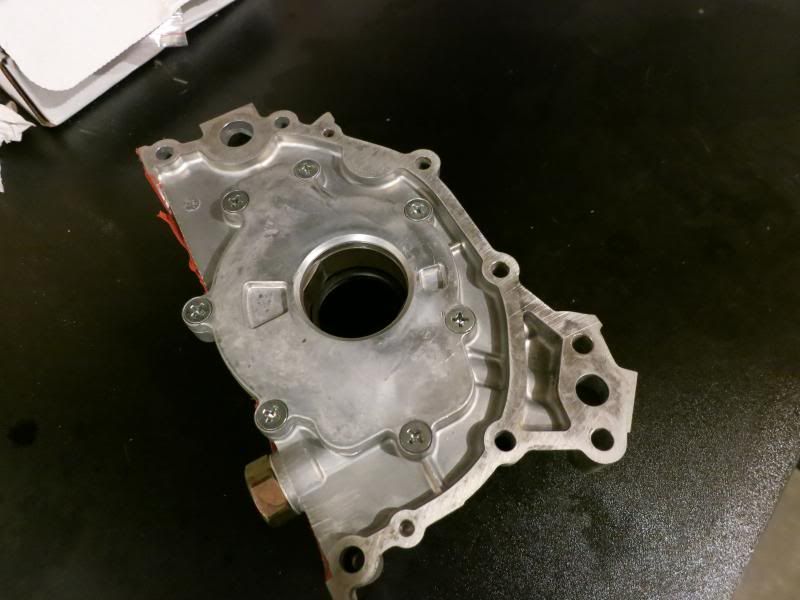
A few seconds later..note the absence of timing marks on the gears.
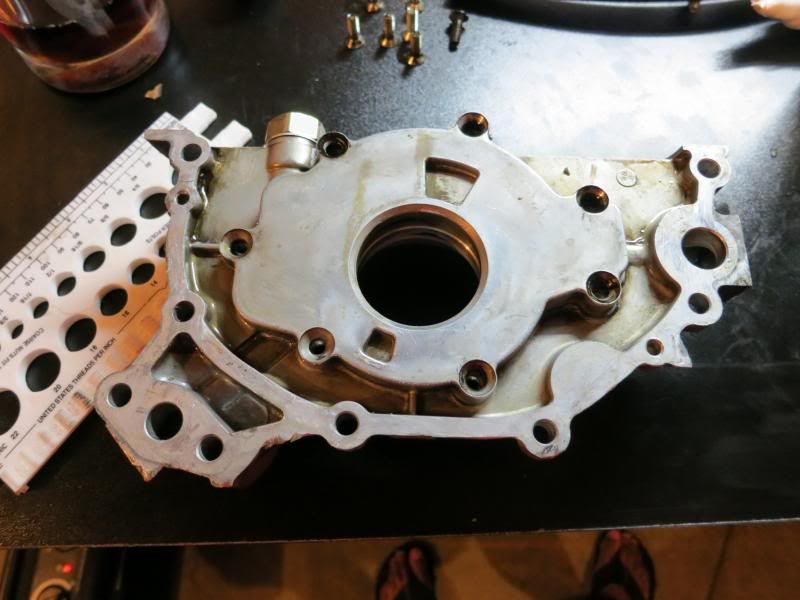

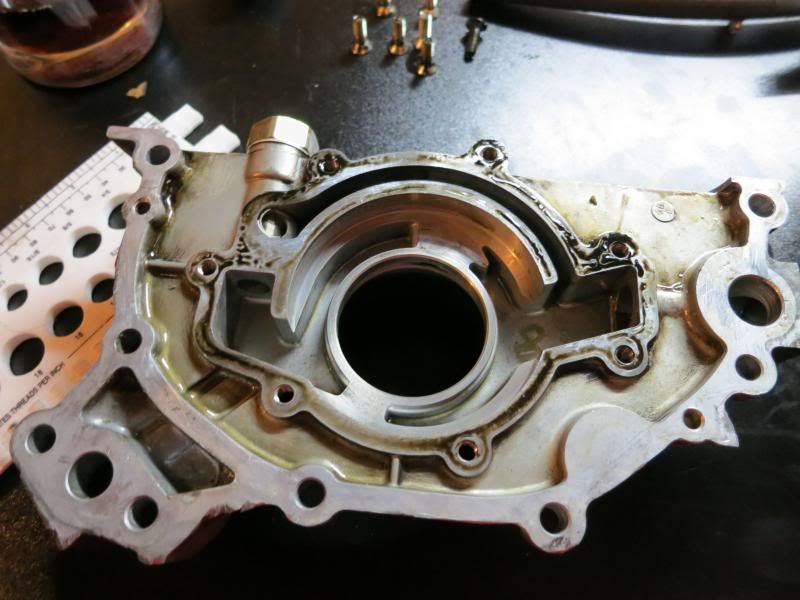
Here is the new set of 81mm Reimax gears.
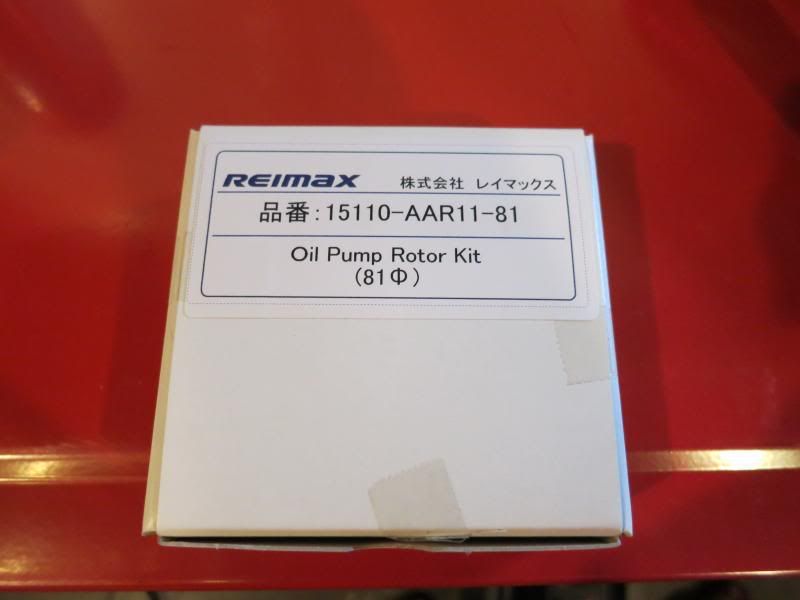
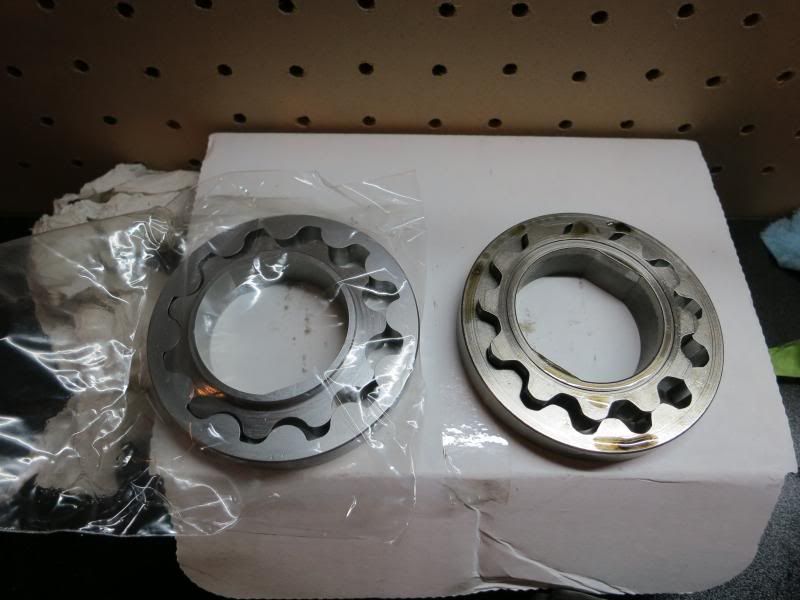
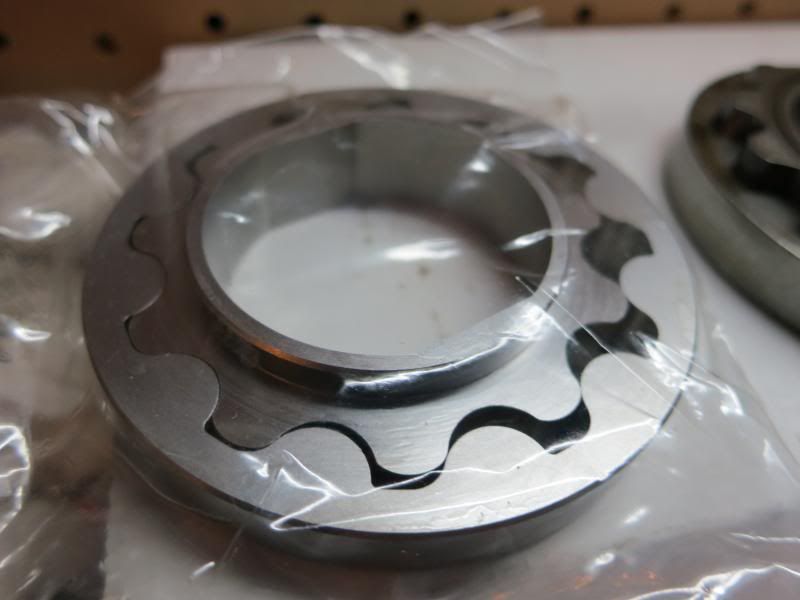
There's only one way for these to go to line up the timing marks.A light smear of oil went on before buttoning up the cover plate.
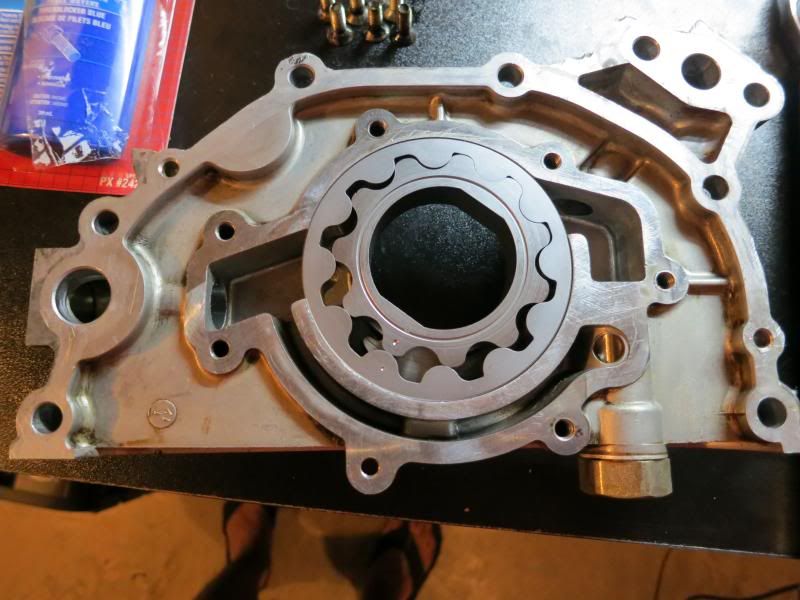
A light smear of medium strentgh blue threadlocker went on each screw. Didn't bother with a torque wrench on these so just went a tad beyond snug.
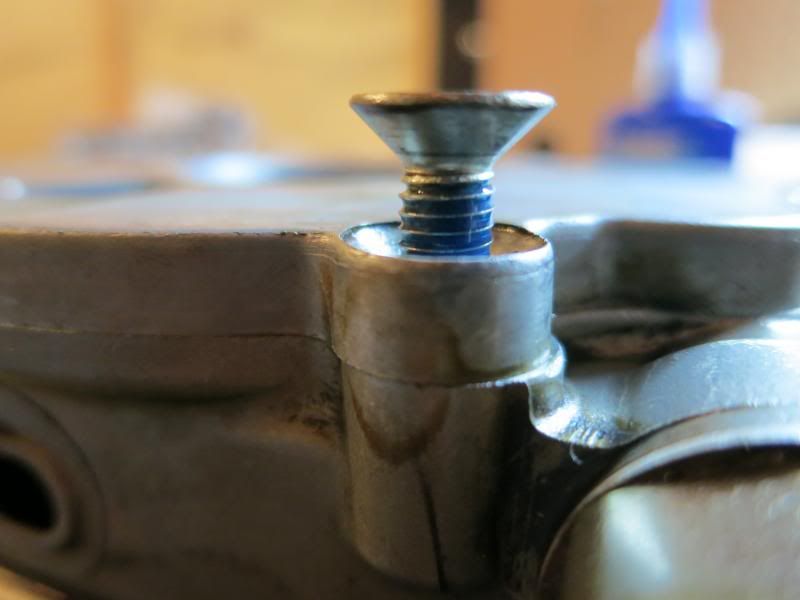
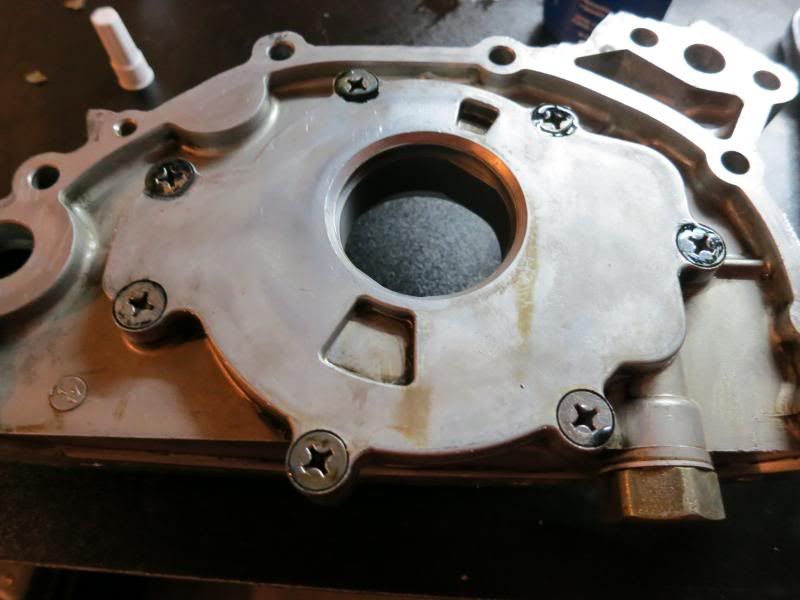
Next I installed a new oil seal. I just coated it in WD40 and pushed it in by hand till it was flush with the pump surface. I will coat it with oil later.
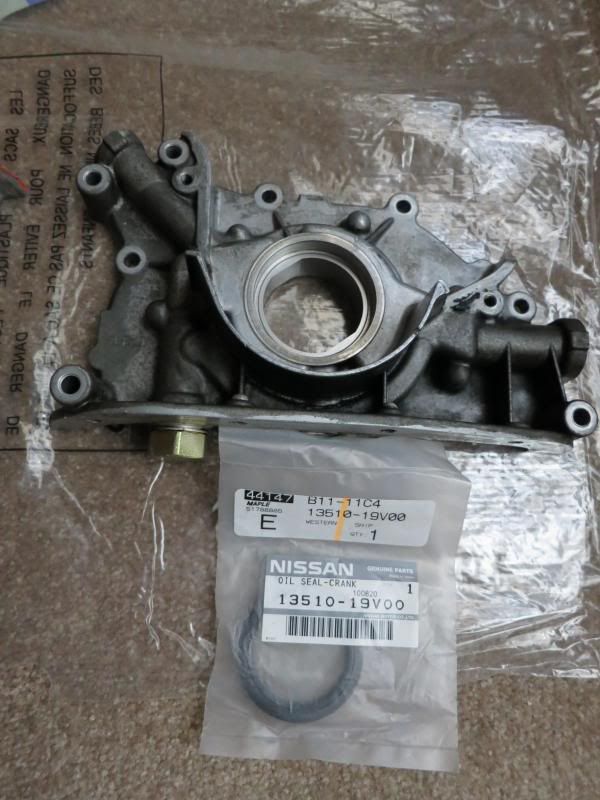
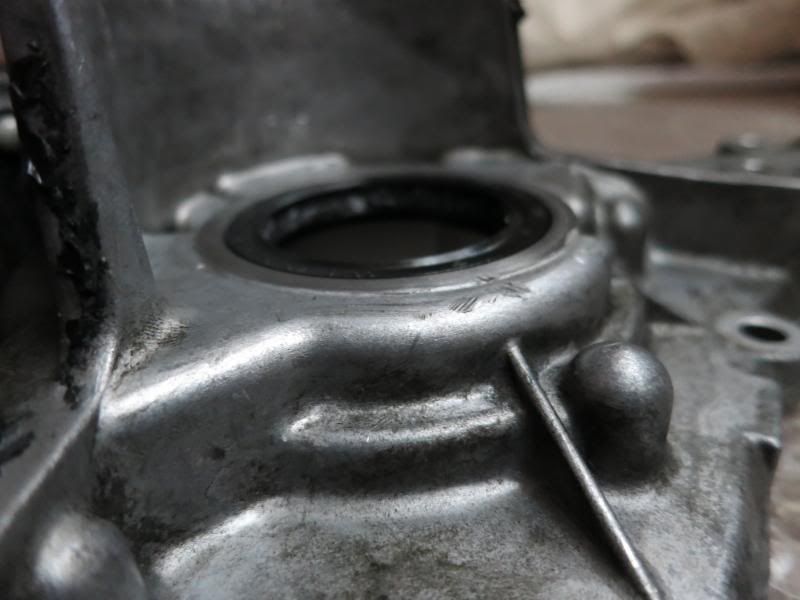
I then cleaned up the remnants of the RTV off the block.
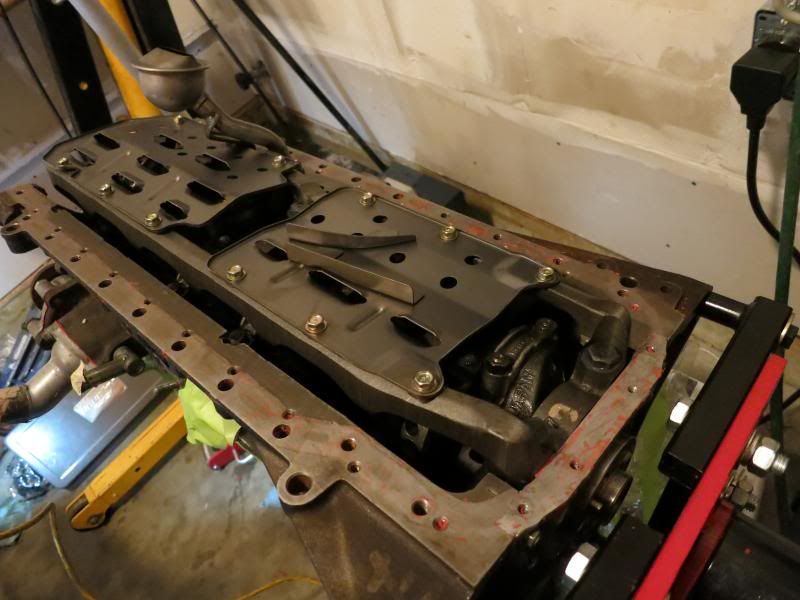
I then bolted up the oil pump to the block, using some gasket sealant of the pump gasket.
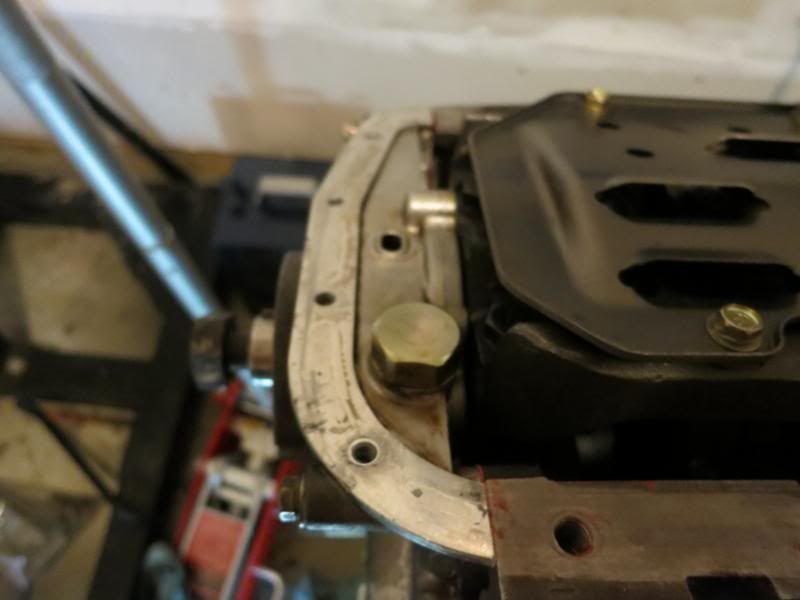
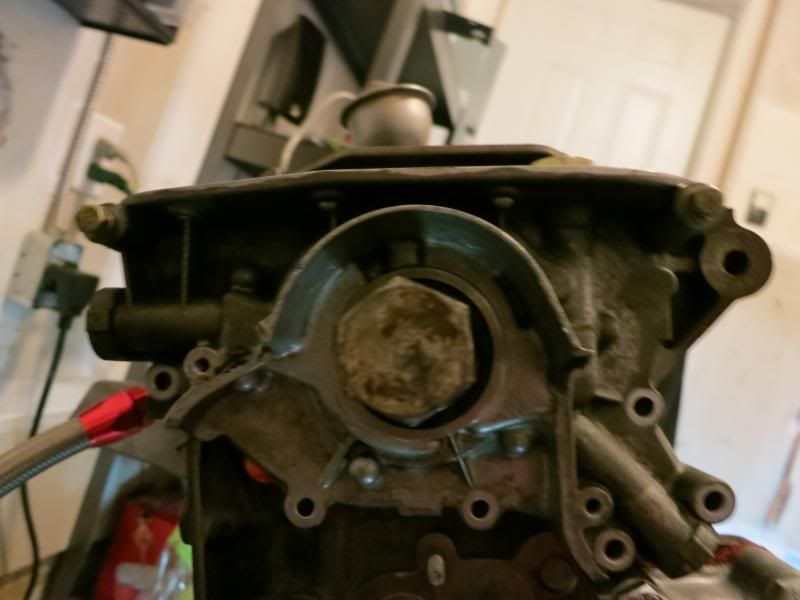
Used some of the good old orange RTV and went to town with it.
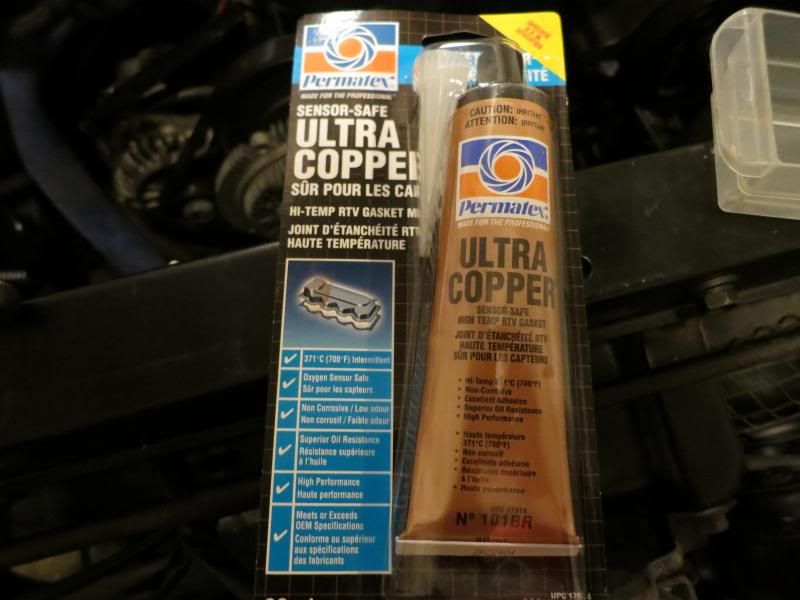
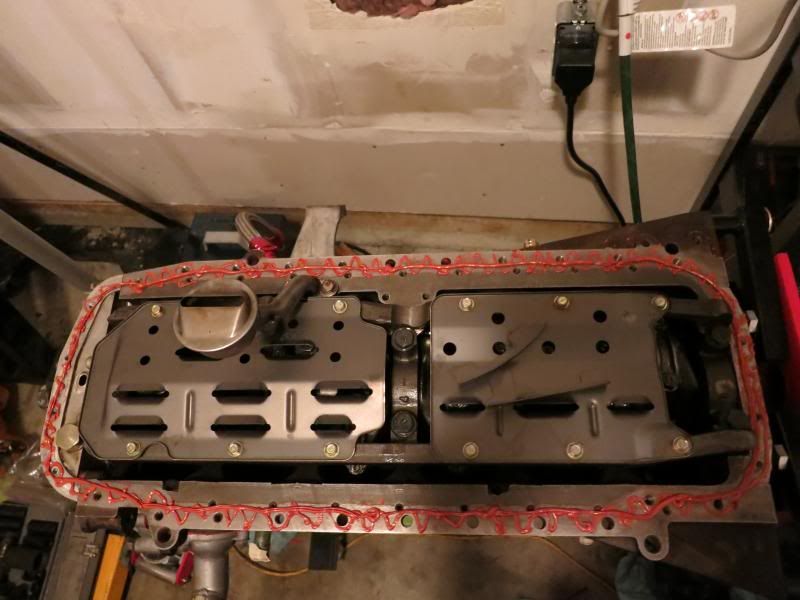
Then put the cover back on and torqued it up to spec.
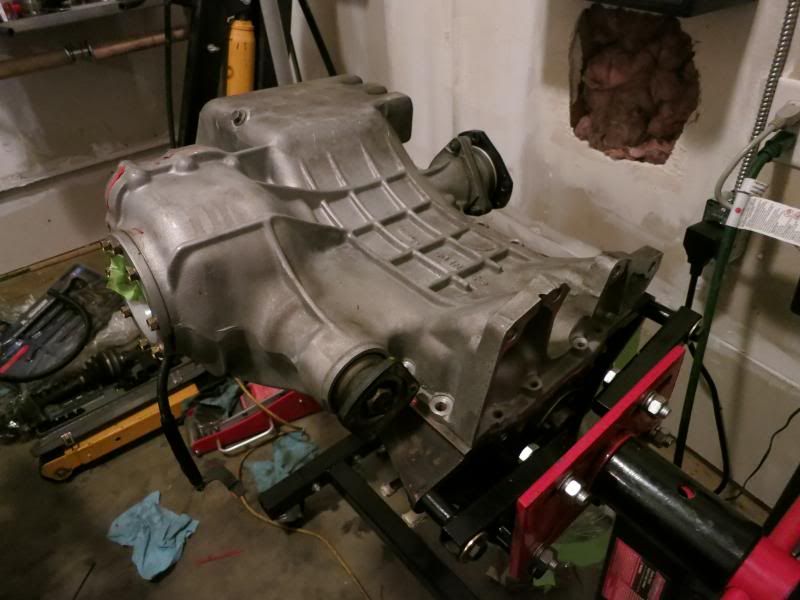
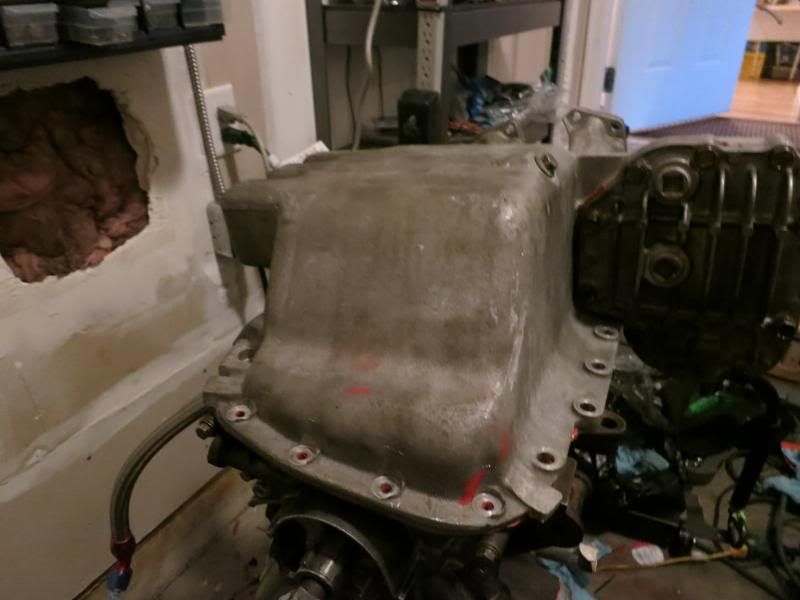
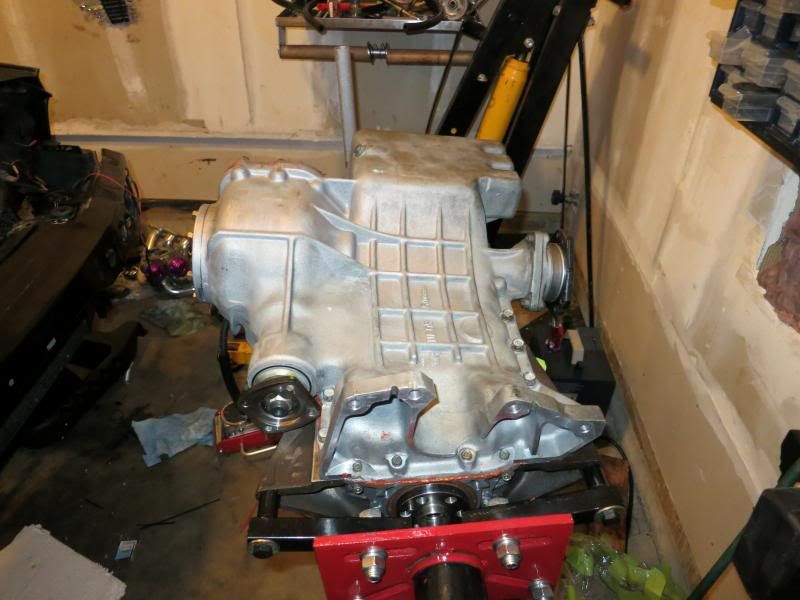
Comment