P/S Reservoir Relocate Part 2
Thanks! I will take a video of her breathing hopefully with soemthing better than a crappy phone cam. She hasn't breathed properly for 2 years now!
Continuing on to something I left a while back, the power steering reservoir relocate to the rad support. I had already cut off most of the stock bracket that holds the reservoir to the strut tower.
I joined the rad support to the reservoir with some shoddy looking welds
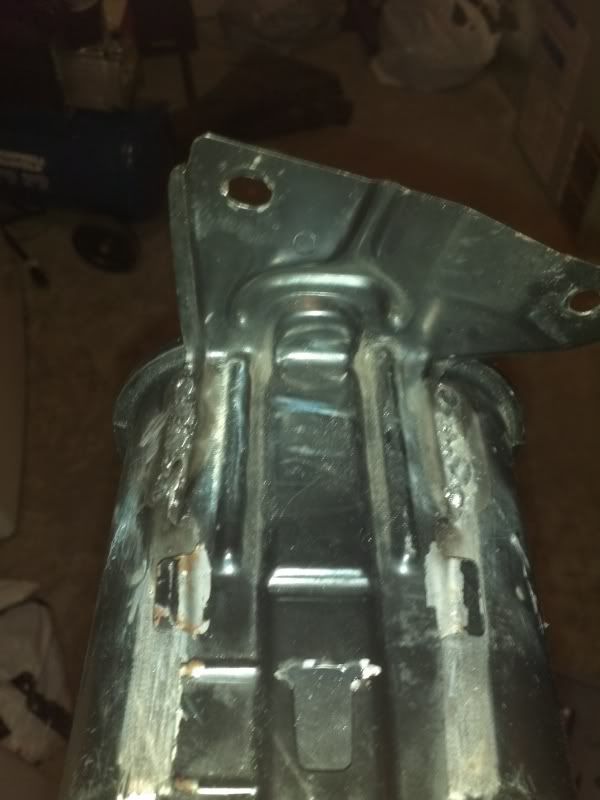
But it fit well at least.
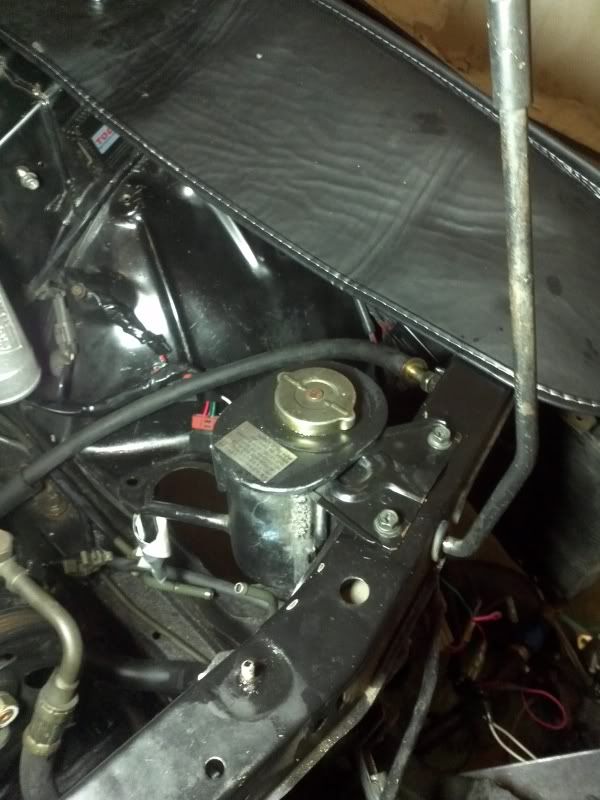
I then had the reservoir blasted over the holidays..so much P/S fluid kept coming out, the guy had to bake out the remaining fluid.
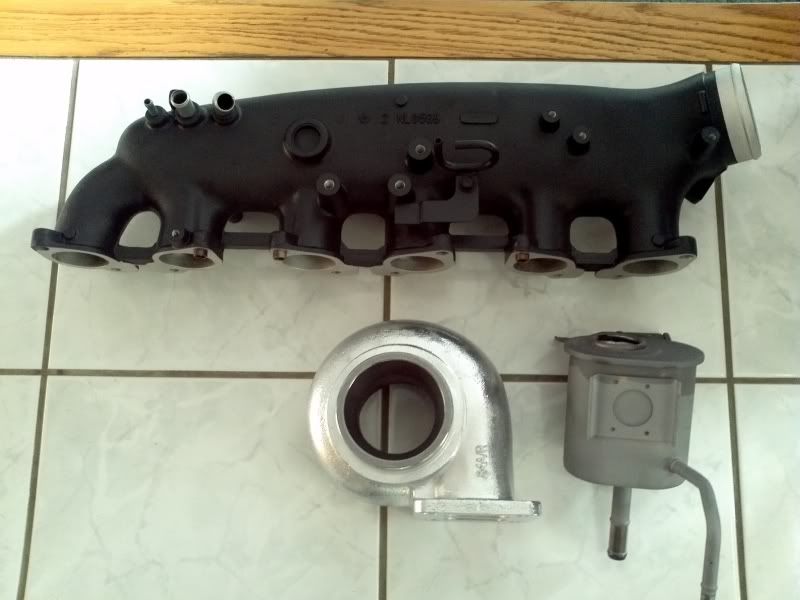
I decided that my welds didnt pass QC, so I hastily covered it up with some epoxy putty.
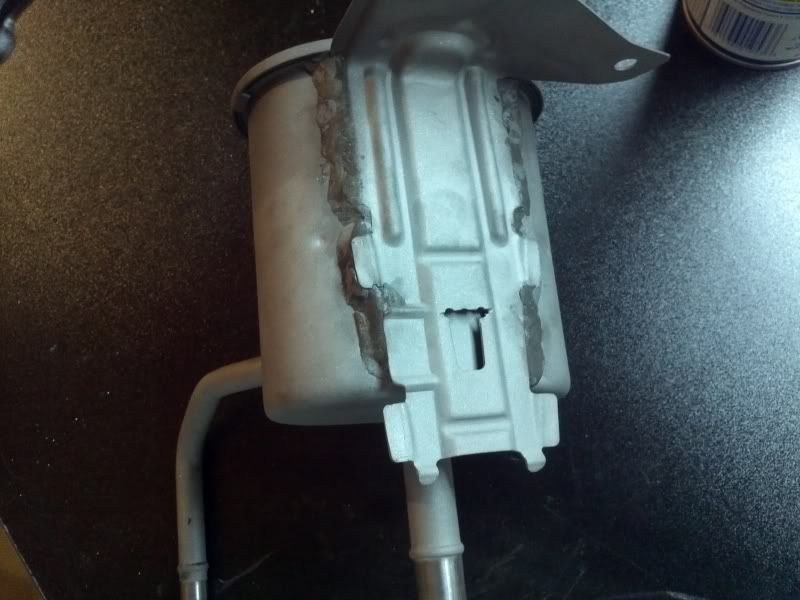
The cap had lost its brass-looking coating so it looked like the rest of the reservoir. Rather than painting it, I opted to polish it.
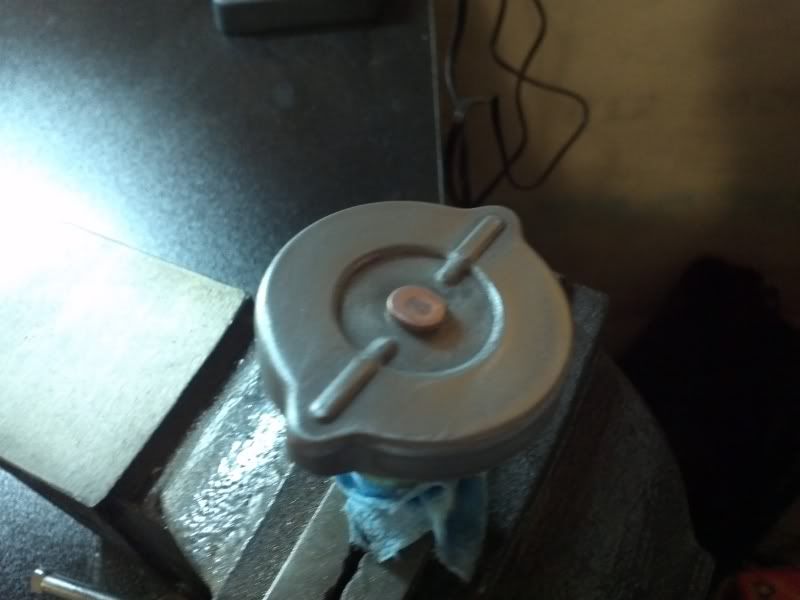
I worked my way up from 100 grit to 1500 grit sandpaper in stages.
I then applied the rubbing compound prior to polishing.

After two step polishing compound for steel and Fluidfilm..obviously it can look a lot better with more time but I didn't want to spend so much time and have it start surface rusting right away..I will employ the time honored wait and see approach before spending more time on it.
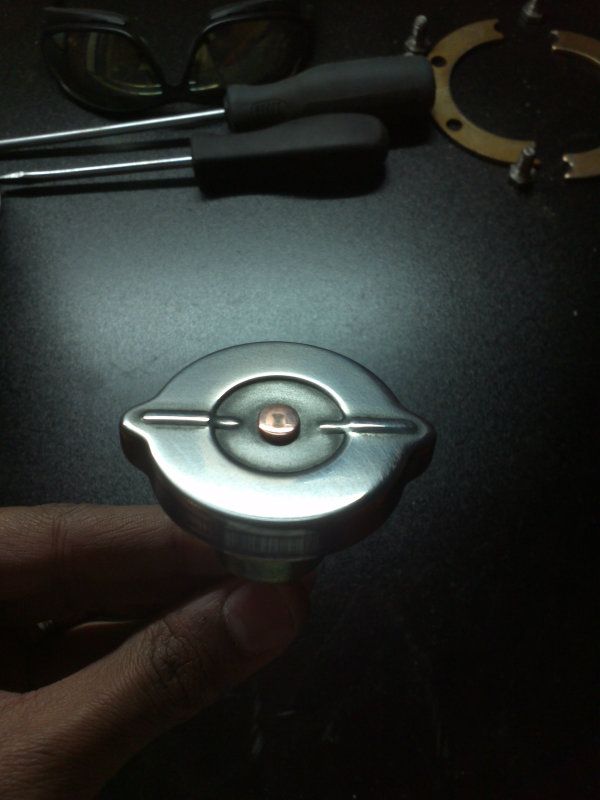
I washed the reservoir and cleaned it thoroughly inside and out in preparation for painting. I painted the reservoir with VHT black caliper paint, and later baked it in the oven for curing.
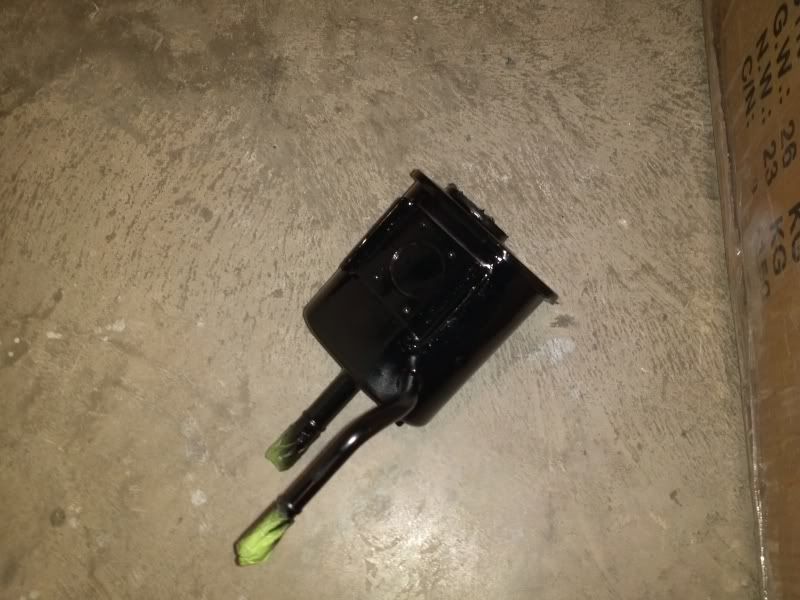
And the final product..
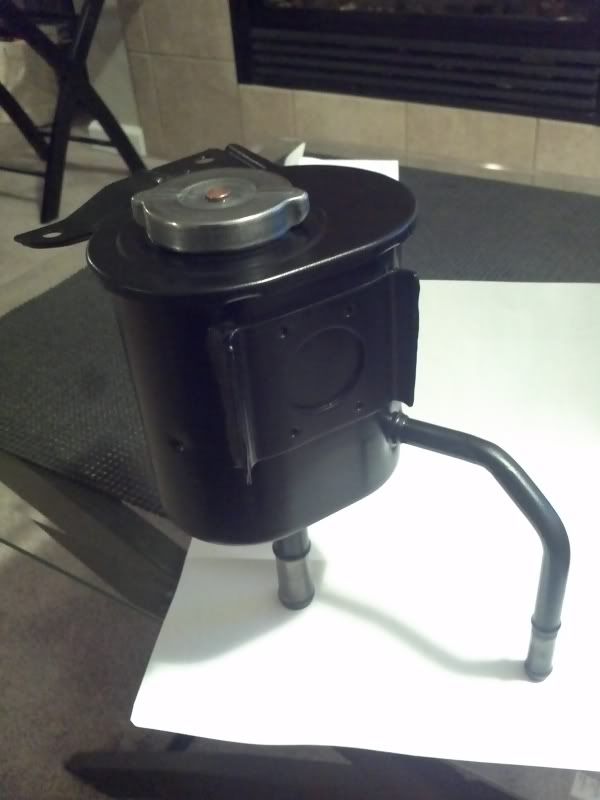
Originally posted by nimblestix
View Post
Continuing on to something I left a while back, the power steering reservoir relocate to the rad support. I had already cut off most of the stock bracket that holds the reservoir to the strut tower.
I joined the rad support to the reservoir with some shoddy looking welds
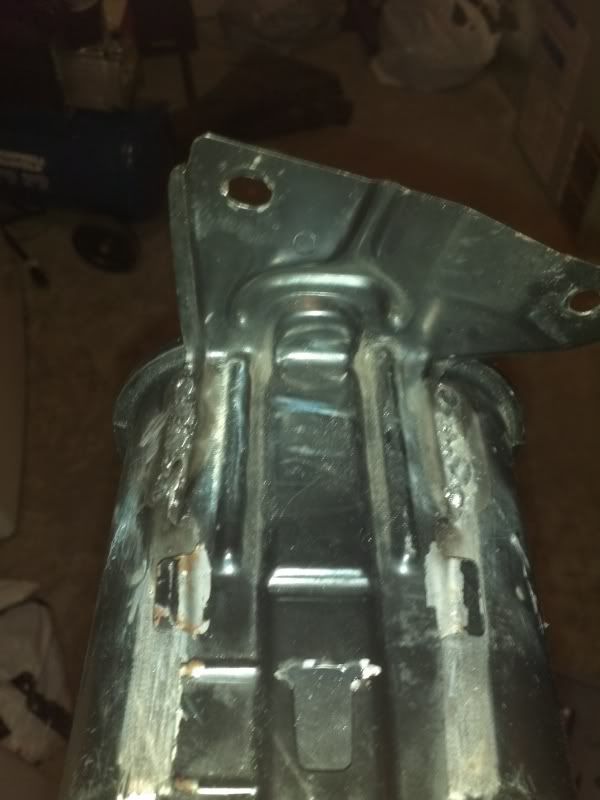
But it fit well at least.
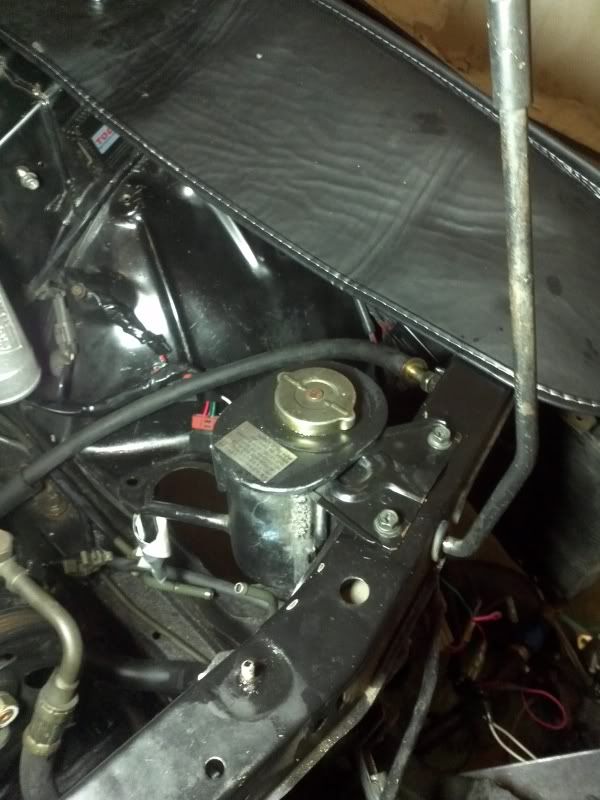
I then had the reservoir blasted over the holidays..so much P/S fluid kept coming out, the guy had to bake out the remaining fluid.
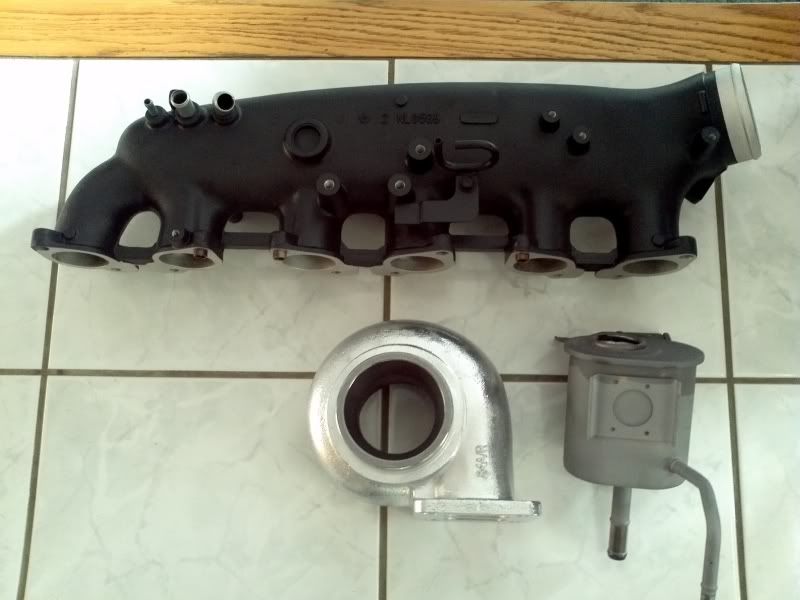
I decided that my welds didnt pass QC, so I hastily covered it up with some epoxy putty.
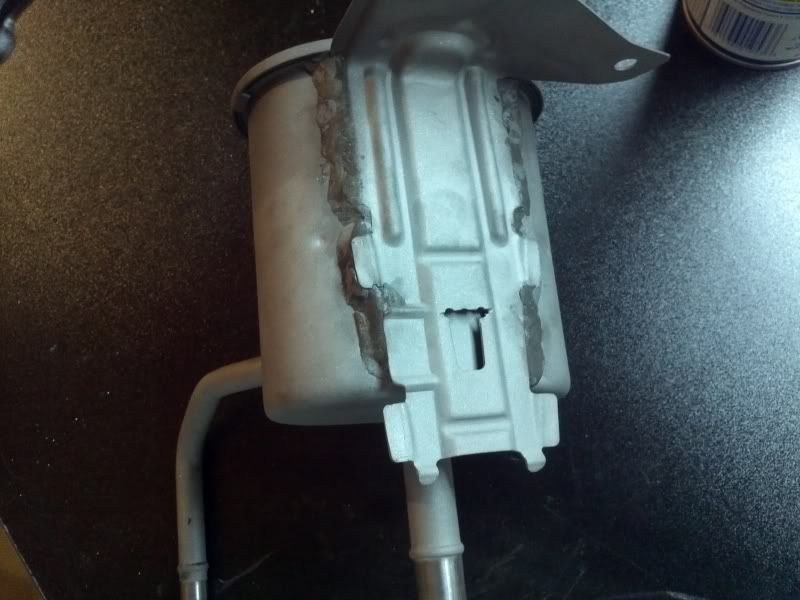
The cap had lost its brass-looking coating so it looked like the rest of the reservoir. Rather than painting it, I opted to polish it.
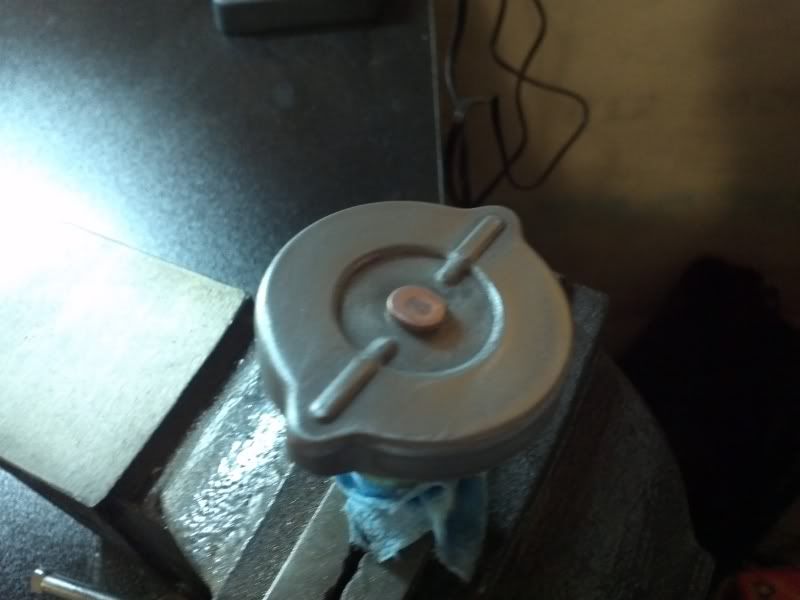
I worked my way up from 100 grit to 1500 grit sandpaper in stages.
I then applied the rubbing compound prior to polishing.

After two step polishing compound for steel and Fluidfilm..obviously it can look a lot better with more time but I didn't want to spend so much time and have it start surface rusting right away..I will employ the time honored wait and see approach before spending more time on it.
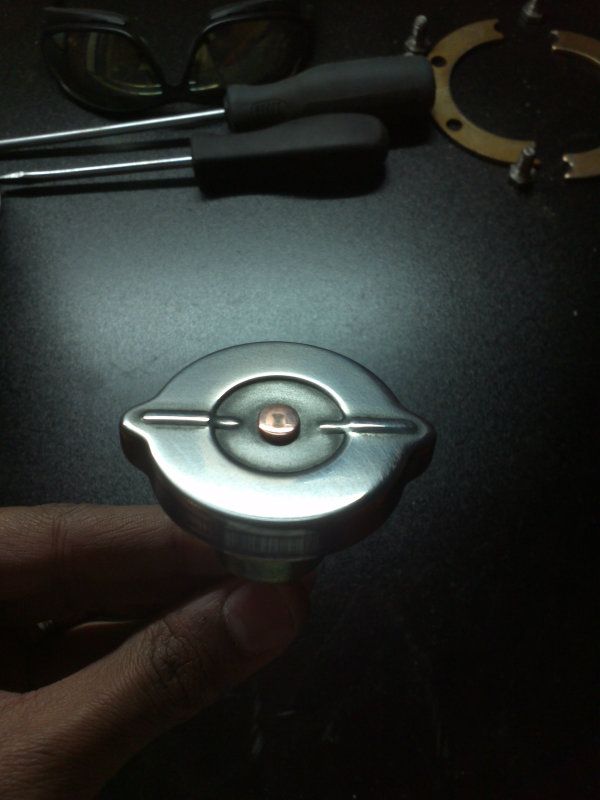
I washed the reservoir and cleaned it thoroughly inside and out in preparation for painting. I painted the reservoir with VHT black caliper paint, and later baked it in the oven for curing.
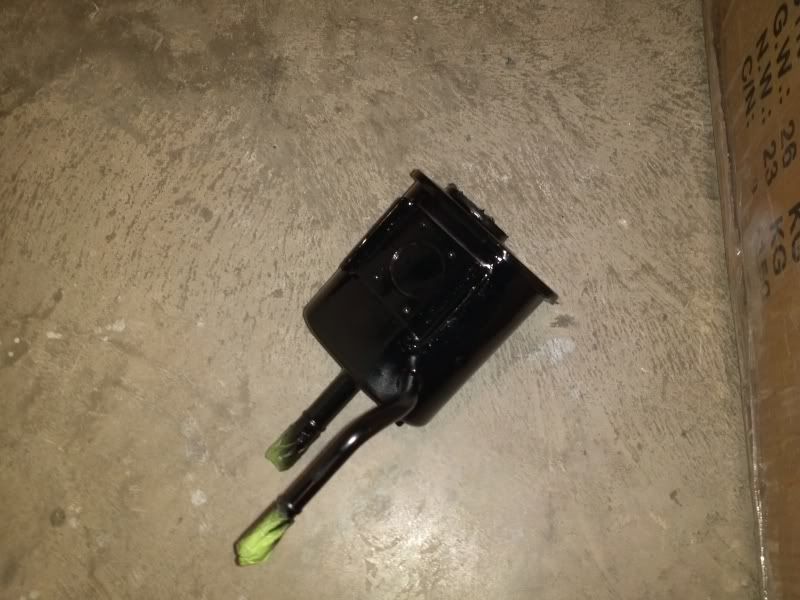
And the final product..
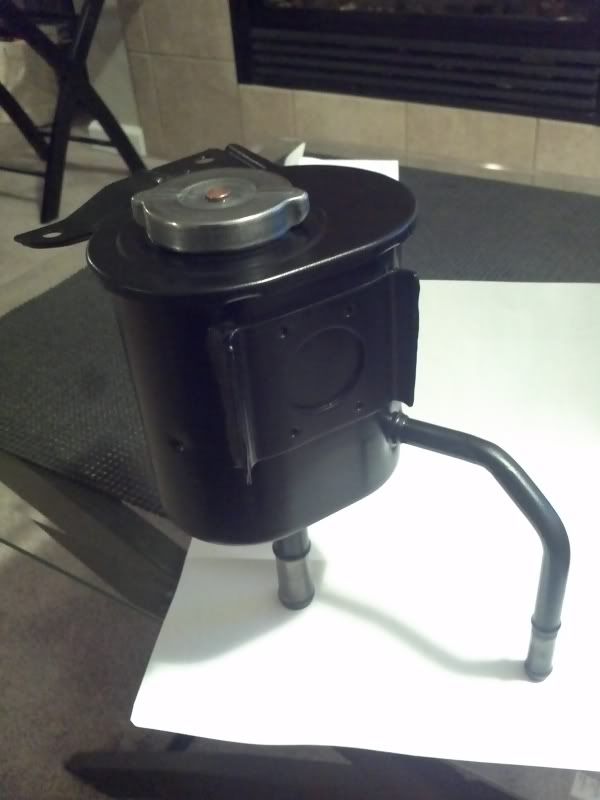
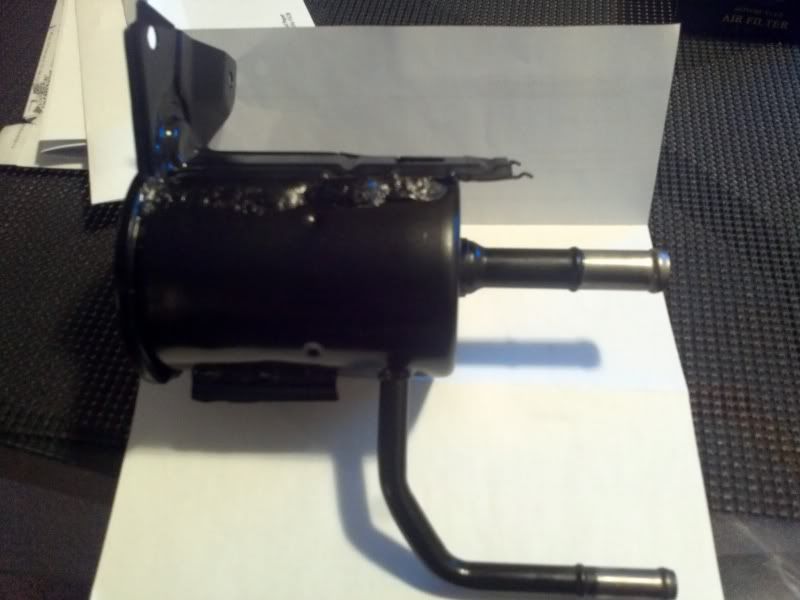
Comment